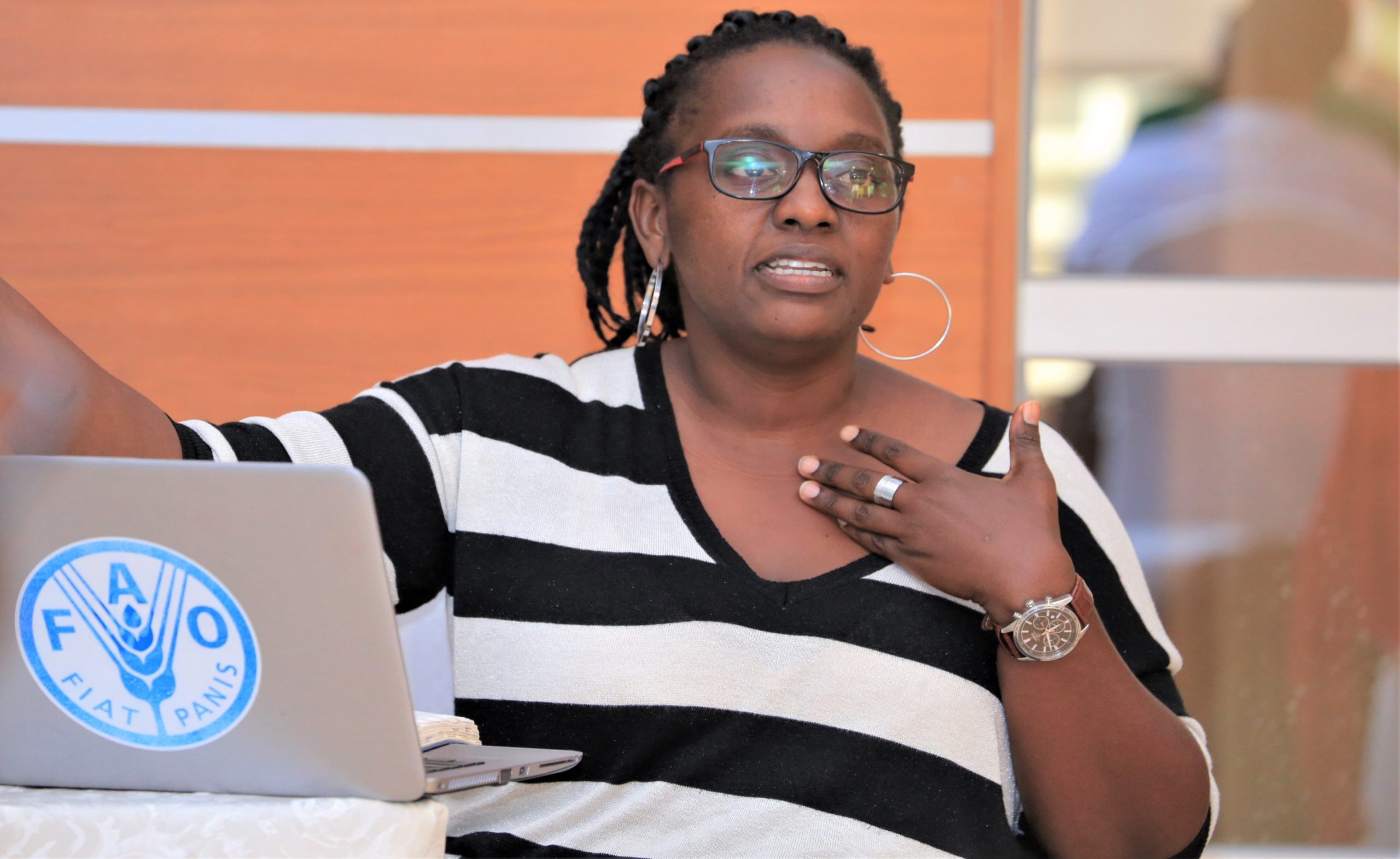
Food and Agriculture Organisation of the United Nations – FAO. (PHOTO/Courtesy)
By Zainabu Kakungulu- Programme Officer,
Food and Agriculture Organization of the United Nations (FAO)
Over the past two decades, growing trees, mainly for timber and poles increasingly became a popular investment venture in Uganda. It is estimated that the area of forest plantations in Uganda has grown from about 3 000 hectares (ha) in 2003 to between 100 000ha – 150 000ha in 2019. Furthermore, approximately 5 000ha are added each year. The expansion of forest plantation estate is expected to continue for the foreseeable future, given the rising demand for wood products, ultimately creating more jobs along the forest value chain.
World over, forestry ranks among the top four most dangerous jobs alongside agriculture, mining and construction. Forestry workers often work long hours and are exposed to safety, health and environmental hazards, including harvesting operations (manual and mechanised), sawmilling, and harmful exposure to pesticides, herbicides and other chemicals. Generally, more than two million people die annually from work-related accidents or diseases and about 317 million suffer from work-related injuries1 .
The World Day for Safety and Health at Work is therefore an opportunity to raise awareness about safety concerns in the forestry subsector and the need to enhance the social, economic and environmental benefits from forestry investment. This year’s theme is “Anticipate, prepare and respond to crises – Invest Now in Resilient Occupational Safety and Health Systems”. This year’s commemoration seeks to raise awareness and stimulate dialogue on the importance of creating and investing in resilient Occupational Safety and Health (OSH) systems to mitigate and prevent the spread of COVID-19 at the workplace.
Status of health and safety in forestry operations in Uganda
In 2019, the Food and Agriculture Organization of the United Nations (FAO) in Uganda commissioned a study to assess the occupational health and safety for forestry operations in Uganda, focusing on sawmilling operations. The study aimed at developing a health and safety strategy for the sawmilling industry in Uganda, which, the study found, is dominated by many small-scale informal sawmills and only a few formal medium scale enterprises. Study findings showed that small-scale sawmillers focus mainly on remaining profitable, paying more attention to direct aspects of the business that reduce costs and improve productivity. All this is at the expense of other considerations such as health and safety of workers, which actually significantly contribute to productivity. To compound this problem, often, workers at small-scale sawmills are usually ignorant of their rights at work and the duties of employers or may not be adequately empowered to seek redress when their rights are infringed upon. Furthermore, government departments responsible for occupational health and safety monitoring in sawmilling have challenges in carrying out their inspection mandate, such as the remote, fragmented and hard-to-reach locations of informal small-scale sawmills.
However, formal medium and large scale sawmill operations have better safety systems, with top-level management commitment to improving safety of workers. These companies were found to have sufficient safety policies, guidelines and safety management systems, as well as Standard Operating Practices (SOPs) to guide operational safety management and the supervision. Workers are also more aware of the importance of safety at the workplace.
Key principles for promoting safety culture for the forestry subsector in Uganda
The safety and well-being of forest workers is an important aspect for the long-term sustainability of the industry. Having in place and implementing a workplace safety programme demonstrates to workers and the public that the organization is socially responsible. Unlike the popular misconception that safety is an unnecessary additional expense to an operation, there’s evidence of substantial cost reduction by implementing a health and safety programme. These include reduced direct costs in compensation to sick or injured workers and lower indirect costs such as production time and output lost due to accidents or absences. Below are some key principles for promoting OSH in forestry operations:
Developing workplace safety policies and procedures
Having an Occupational Health and Safety Policy communicates commitment to workplace health and safety. The policy should address key aspects such as the aims and objectives, indicate specific roles and responsibilities for safety and health at all levels of the operation, clarify how risks are managed and i.e. how the organization plans to deal with competing priorities such as production.
Developing a system of accountability for all levels of the organization
Leadership and management should be committed to implementing and constantly improving safety in the operation. Everyone must play by the same rules and be held accountable for their areas of responsibility. Signs of a strong culture manifest in individuals holding themselves accountable.
Training workers
Carelessness and human error account for over ninety percent of workplace accidents. Unsafe behaviour such as using unsafe shortcuts to complete tasks, working under the influence of substances such as alcohol, using inappropriate Personal Protective Equipment (PPE) result into increased risk of accidents in forestry. In addition, systems, processes and rules of forestry work may unintentionally promote unsafe behaviours through ineffective work policies and procedures that ignore the workplace safety. It is important that workers do not become complacent with health and safety procedures, and to remember that no workplace is 100% safe. Ensuring that all workers undergo health and safety training can help reduce accidents and injuries in the workplace.
Listed below, are some of the most important steps to reduce accidents in forestry
? Hazard identification and risk control: determine which hazards are present in the workplace and take steps to eliminate or minimize them.
? Safe work procedures: describe in writing, or by other means, how to carry out specific tasks safely. Videos can be very useful.
? Orientation, education, training and supervision: prepare workers for the job and make sure they continue to work safely. This is particularly important for new and young workers.
? Safety inspections: identify workplace hazards so they can be eliminated or controlled.
? Incident investigation: find out why an accident or injury occurred so the causes can be corrected.
? Health and safety meetings: provide an opportunity for workers and supervisors to communicate any concerns about workplace health and safety.
? First aid: determine what level of first aid equipment is required for the workplace and make sure everyone knows what to do if someone is injured on the job.
? Records and statistics: maintain documentation to help identify recurring problems and ensure that hazardous conditions are corrected.
?
SAFETY DOESN’T COST, IT PAYS
1 Estimating the Economic Costs of Occupational Injuries and Illnesses in Developing Countries: Essential Information for Decision-Makers. Working Paper 2012. International Labour Organization (ILO), Geneva.
2 McEwan, A. 2019. Occupational health and safety strategy for sawmilling industries in Uganda. Kampala, FAO [forthcoming]
3 Garland J., Cedergren J., Eliasson L., van Hensbergen, H., McEwan, A. and Wästerlund, D. 2020. Occupational safety and health in forest harvesting and silviculture – A compendium for practitioners and instructors. Forestry
Working Paper No. 14. Rome, FAO. https://doi.org/10.4060/ca8773en